Was treibt das Unternehmen Ossiform an?
Bei Ossiform in Dänemark dreht sich alles um die Konstruktion von patientenspezifischen Knochenimplantaten per 3D-Druck.
Angefangen als Studentenprojekt, war es immer die Vision, Patienten in Not zu helfen, indem sie hochwertige medizinische Geräte in Form ihrer P3D Bone-Lösung liefern – auf den Patienten abgestimmte resorbierbare Knochenimplantate, die die natürliche Bildung neuer Knochen erleichtern, um Knochendefekte bei Patienten zu rekonstruieren.
P3D Bone basiert auf reiner Biokeramik und wird mit einer einzigartigen knochenähnlichen Porosität gedruckt, die ein effektive Umformung in den natürlichen Knochen ermöglicht. Das Ergebnis ist ein natürlicheres Implantat in Bezug auf Material, Form und Struktur. Mit P3D Bone sind Chirurgen in der Lage, ein Implantat bereitzustellen, das genau auf die Bedürfnisse des Patienten abgestimmt ist, und dadurch die Ergebnisse für den Patienten zu verbessern, die Effizienz des Verfahrens zu erhöhen und das Risiko von Komplikationen zu minimieren.
3D-Druck und 3D-Scannen gehen Hand in Hand
Der Prozess des 3D-Drucks ist eng mit der Qualitätskontrolle verbunden, um sicherzustellen, dass die gedruckten Produkte mit dem geplanten Design übereinstimmen. Für seine Knochenimplantate durchläuft Ossiform eine Reihe entscheidender Schritte, um die vorgegebenen Spezifikationen des Implantatdesigns für eine erfolgreiche, auf den Patienten abgestimmte Knochenrekonstruktion zu erfüllen. In den Prozess sind mehrere Iterationsschleifen und der GOM Scan 1 zur Qualitätssicherung eingebunden.
1. CT-Daten des beschädigten Körperteils
Der Prozess beginnt, wenn ein Patient einen beschädigtes Körperteil hat, das mit Knochenimplantaten repariert werden muss. Die Knochendefekte werden anhand von CT-Daten erkannt und bildet die Grundlage für die Arbeit bei Ossiform.
2. Implantatdesign
Nach Erhalt der CT-Daten beginnt Ossiform mit der Entwicklung eines Implantats, das den individuellen Anforderungen des Knochendefekts des Patienten entspricht. Das Implantat wird in Zusammenarbeit mit dem Chirurgen, der den Eingriff vornimmt, in mehreren Schritten geprüft, um sicherzustellen, dass es alle Anforderungen für die Implantation in den Körper des Patienten erfüllt.
3. 3D-Druck von Implantaten
Nach Abschluss des Designprozesses wird das 3D-Druckverfahren des Medizingeräts in einem Reinraum zum Leben erweckt.
4. Mehrere Iterationen der Qualitätskontrolle
Um eine exakte Anpassung an den Knochendefekt des Patienten zu gewährleisten, ist es unerlässlich, dass das Produkt während des gesamten 3D-Druckprozesses innerhalb der Toleranzen liegt. Die Qualitätskontrolle muss daher vor und nach der Nachbearbeitung des Knochenimplantats durchgeführt werden, um die Spezifikationen des Produkts ständig zu überprüfen. GOM Scan 1 hilft hier, die Qualität hoch zu halten und gleichzeitig die Vorlaufzeiten für die Implantat-Lösung zu reduzieren.
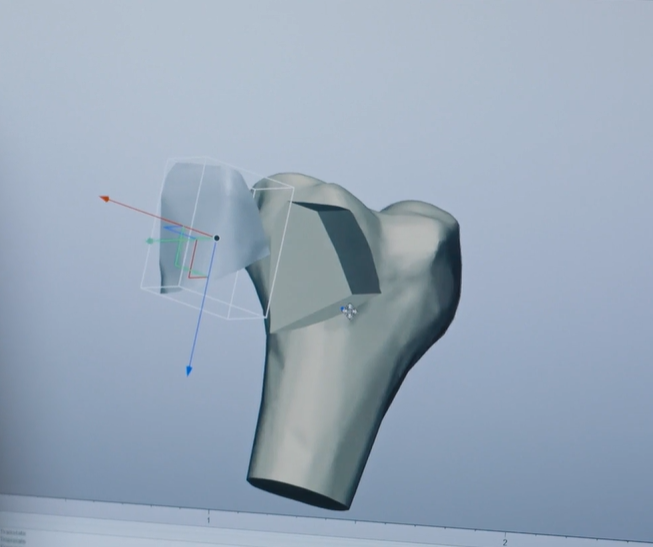
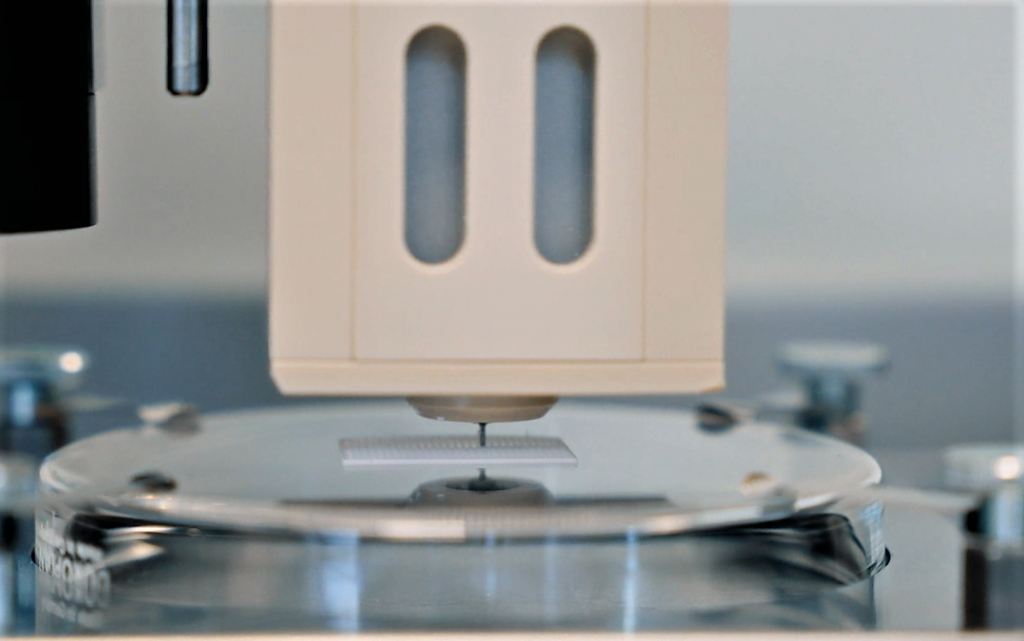

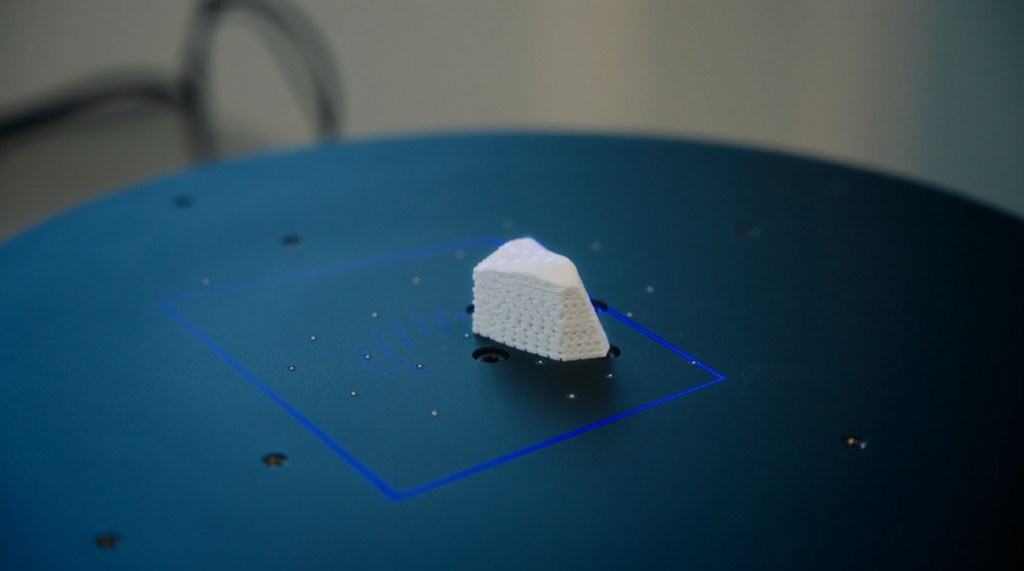
GOM Scan 1 für komplexe und vielseitige Aufgaben
Die Entscheidung von Ossiform, mit GOM Scan 1 zu arbeiten, war das Ergebnis von Gesprächen mit unserem dänischen Partner Zebicon, der Ossiform bei der Auswahl und Implementierung des Systems beraten und unterstützt hat. Dies führte zu einer schnellen und einfachen Produktvalidierung im Unternehmen. Der 3D-Scanner ermöglicht es dem Unternehmen, auch komplexe Strukturen von variierenden Implantaten zu scannen. Die Hauptaufgabe besteht hier darin, in zwei Schritten zu prüfen, ob die Abmessungen stimmen.
1. Qualitätskontrolle von 3D-gedruckten Teilen
Nach dem Druck des ersten Knochenimplantats wird GOM Scan 1 verwendet, um die Qualität des 3D-Drucks zu überprüfen. Vordefinierte Toleranzen werden vor der weiteren Bearbeitung des Objekts kontrolliert.
2. Qualitätskontrolle des fertigen P3D-Knochens
Nach dem Sintern des Implantats muss eine Überprüfung der endgültigen Kompatibilität der Spezifikationen erfolgen. Dadurch wird die individuelle Anpassung an den Patienten vor der Implantation sichergestellt.
Die optische Lösung GOM Scan 1 erweist sich als äußerst nützlich, da sie eine Zeitersparnis bei der Qualitätskontrolle ermöglicht. Die einfache Einrichtung macht die Überprüfung der Implantate intuitiv und effizient. Das kompakte Design des Systems ist außerdem perfekt auf die Anforderungen eines Reinraums abgestimmt, in dem der Platz begrenzt sein kann. Darüber hinaus sind die erfassten Daten von höchster Qualität und machen so selbst kleinste Abweichungen sichtbar, die erkannt werden müssen, bevor das Implantat die Produktion verlässt.
Datenauswertung für exakte Passgenauigkeit
Durch den mehrstufigen Produktionsprozess von Medizingeräten sind Abweichungen von der geplanten Konstruktion möglich. Mit Daten, die auf die hochindividuellen Implantate zugeschnitten sind, lassen sich entscheidende Informationen über die Teilequalität ermitteln. In der ZEISS Quality Suite werden Abweichungen im Handumdrehen sichtbar gemacht, um sicherzustellen, dass die produzierten Medizingeräte innerhalb der Spezifikation liegen. Ein weiterer Vorteil der Prüfsoftware: Die Messergebnisse können als PDF-Report exportiert und im Qualitätsmanagementsystem gespeichert werden. Auf diese Weise wird das fertige Implantat aus mehreren Perspektiven geprüft, um sicherzustellen, dass es dem geplanten Design entspricht und perfekt in den Knochendefekt des Patienten passt.
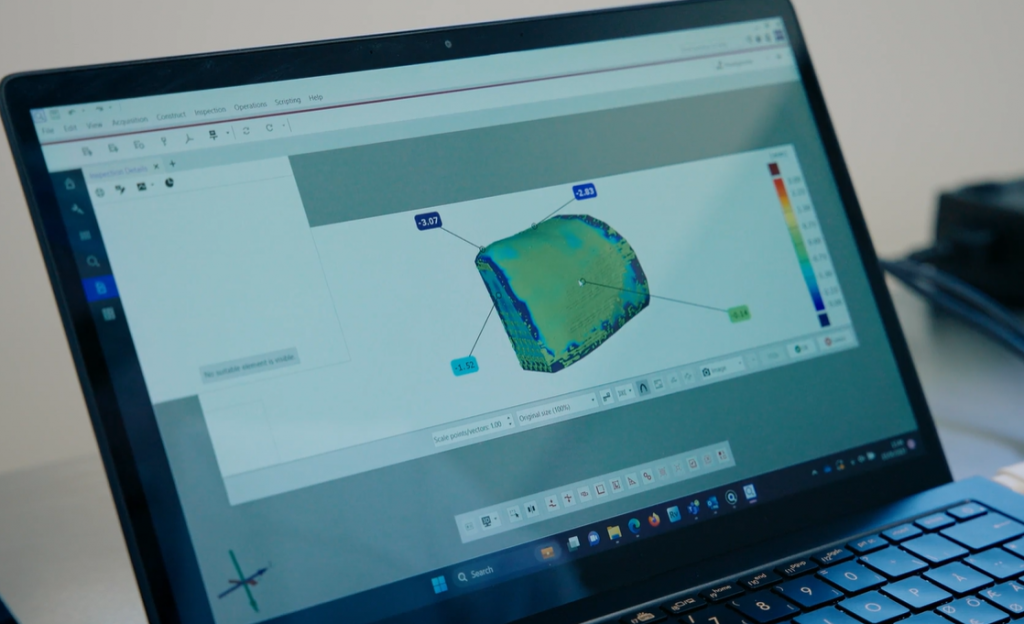
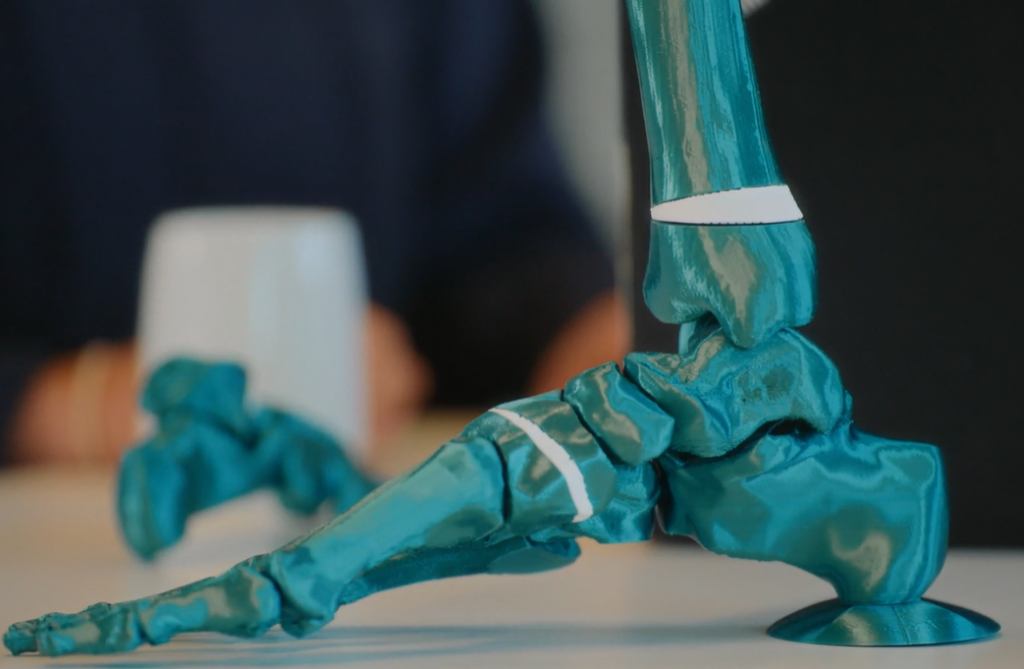
Verfolge die Arbeit bei Ossiform
Du möchtest mehr über die Ideen des Unternehmens und seine Art der Qualitätskontrolle für medizinische Implantat-Lösungen erfahren? Sieh‘ dir hier unsere neueste Maker Story an:
Ossiform: Quality control of 3D printed bone implants
Erfahre mehr über GOM Scan 1
Du bist neugierig auf unsere 3D-Scanlösung und möchtest alles darüber erfahren?
Kontaktiere jetzt deinen Händler vor Ort für weitere Informationen