Implants from CADskills
Founded in 2016 as a result of clinical needs from an operating room, CADskills develops and produces custom-made implants based on clinical CT or CBCT data. The company wants to help the patients with perfectly fitting and fully functioning CADCAM implants. At the same time, the surgeons only require one service provider taking care of all the steps along the way.
The biofunctionalized implants, made specifically for dysfunctional joints and bones, are designed and printed in house. CADskills uses only Titanium gr23 ELI as a material for their implants to avoid the threat of allergic reactions, like it is with typically used materials.
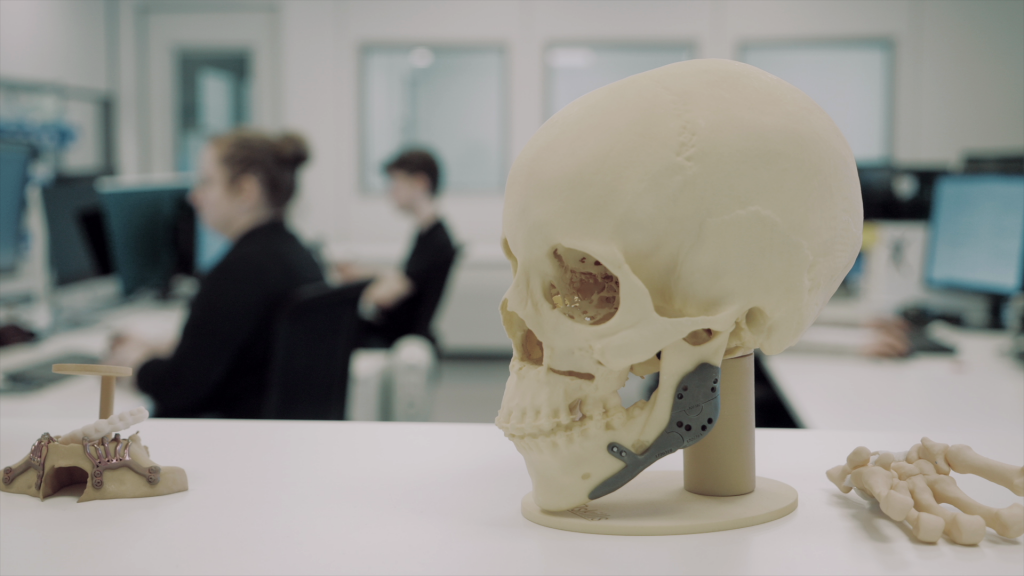
Additive manufacturing of implants
1.
CADskills receives the CT or the CBCT data from the hospital. The surgeon is providing additional information about the case.
2.
CADskills is creating the design of the implant according to the received data and the surgeons preferences.
3.
After the approval of the surgeon, the implant is 3D printed. To resemble similar properties as human bones and facilitate bone ingrowth, the printed implant has a porous structure.
4.
The surface of the implants is treated in the post processing to increase the biocompatibility. Treatments include micro-shot peening, acid etching, ultrasonic cleaning and polishing.
5.
As the last step the implant is scanned with ATOS Q to make sure that the implant quality is good and that there are no deformations.
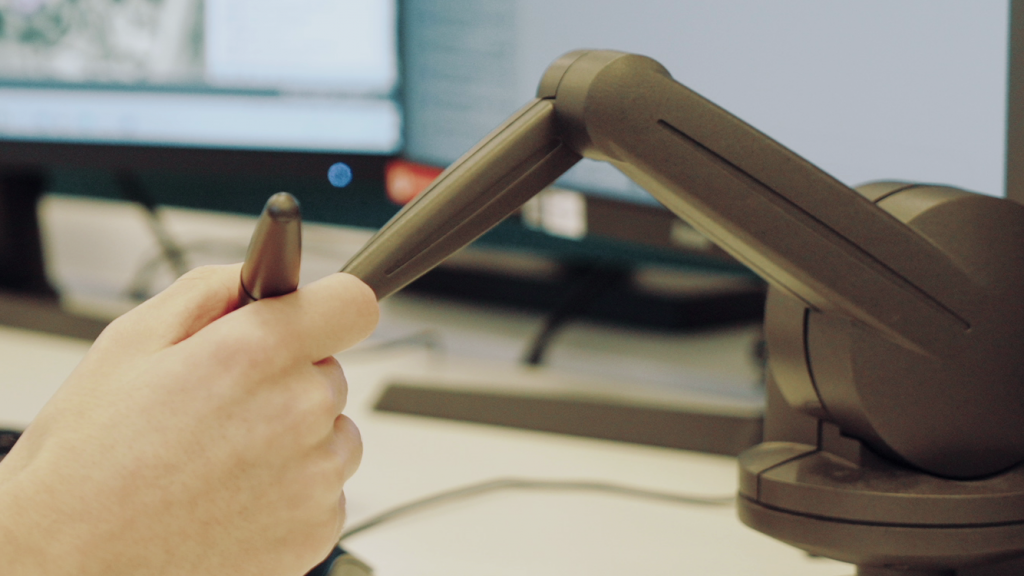
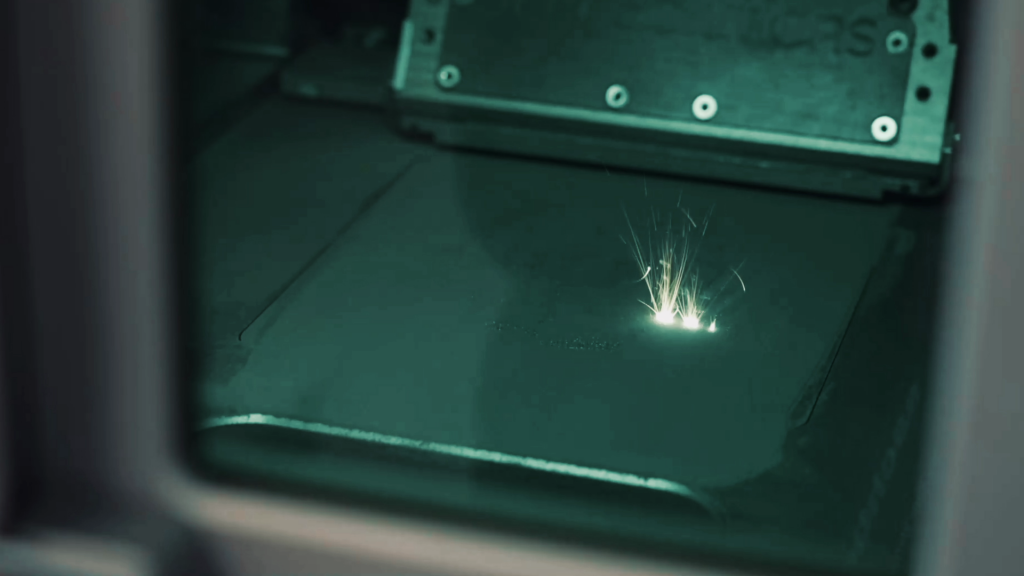
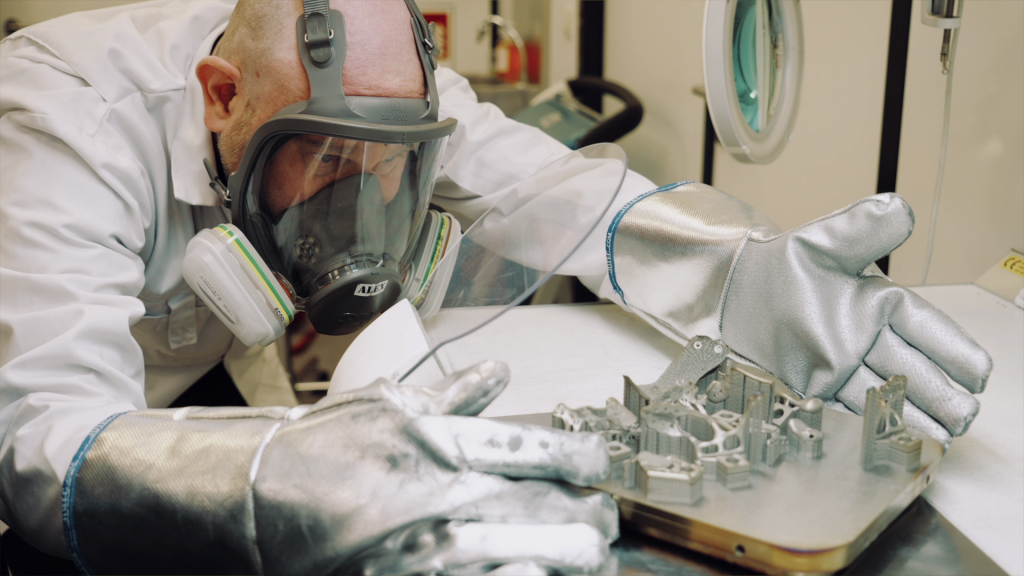
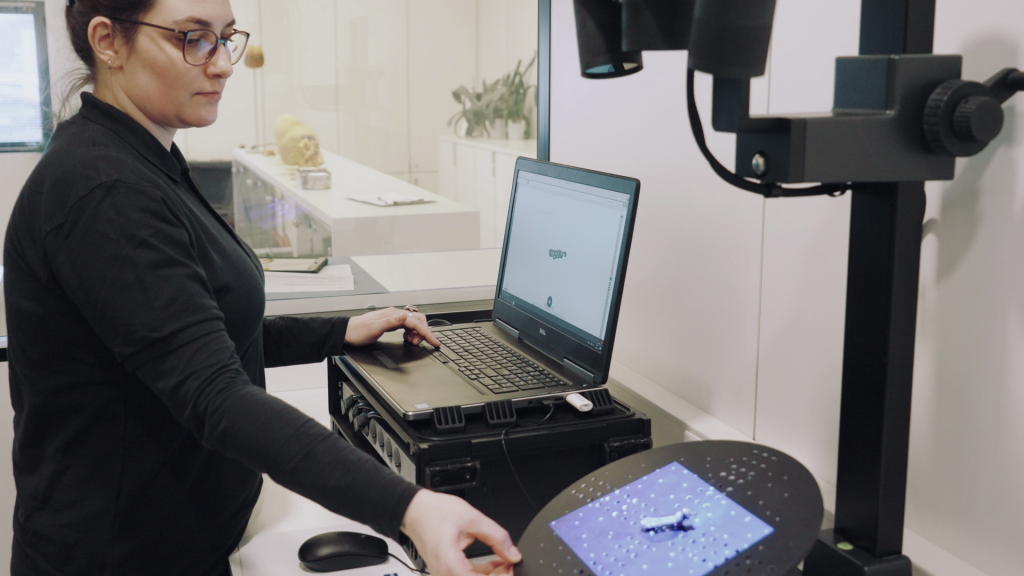
Quality control with ATOS Q
All implants are scanned before they are sent to the hospitals and implanted into the patients. It’s important to check that there are no deformations after the printing and the manual processing. The implant has to have the same dimensions as the 3D design to ensure perfectly fitting implants. Having a high implant quality is important to CADskills, because it ensures durability, compatibility, and reliability with less risks of complications, infections and failure of the implants.
CADskills chose the ATOS Q for this, because it captures data fast while delivering precise results. Its Blue Light Equalizer and Triple Scan Principle are ideal for scanning the reflective surfaces and porous structures of the implants.
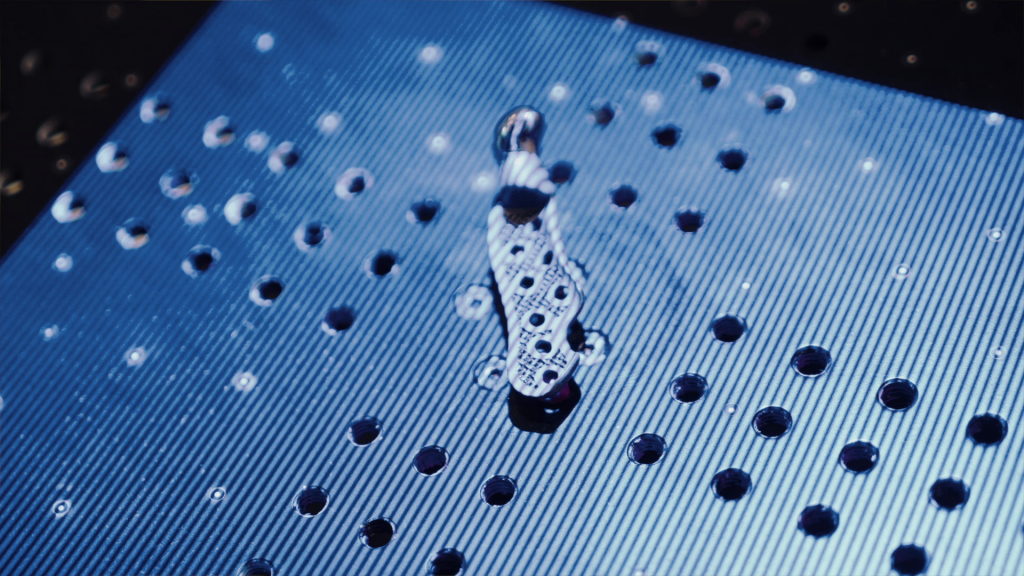
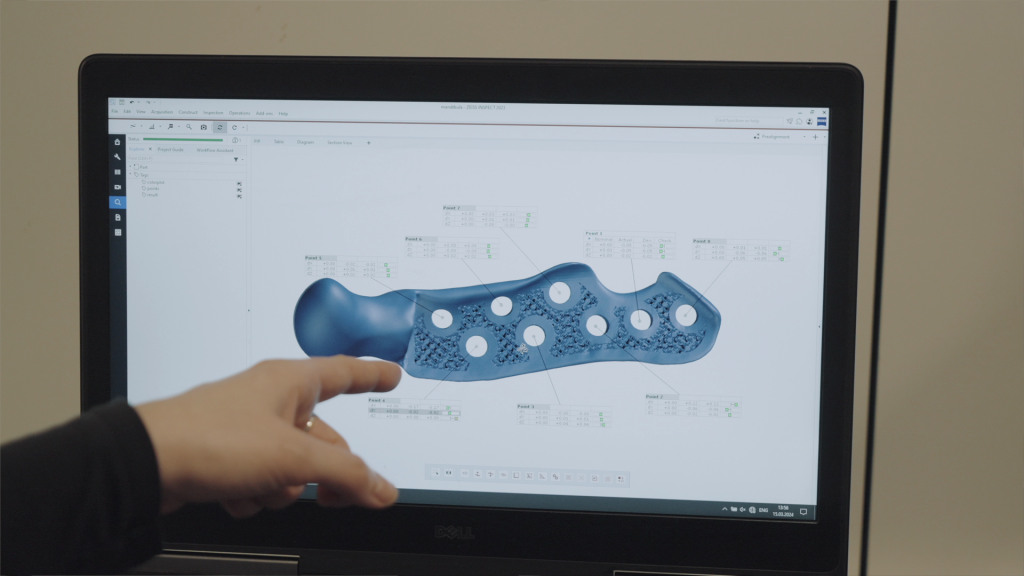
What fascinates me about 3D scanning is that we can scan all our implants, and we can directly see if there is any deviation in color. So, we are grateful and satisfied that we are giving an opportunity to make someone happy and also giving a better life.
Mario Bundo, Chief Operation Officer, CADskills
Follow the work at CADskills
Watch our Maker Story here and discover more about CADskills and the manufacturing of their customized implants:
CADskills: Improving patient specific implants
At CADskills it’s all about custom made implant solutions. Based on CT data, the company designs and develops biofunctionalized implantable devices for dysfunctional joints and bones. To further improve the quality control of their products they use ATOS Q. Have a look at the work of our customer in Belgium to get all the details.
Want to learn more about CADskills? Visit https://www.cadskills.be/en/
Learn more about ATOS Q
Discover more
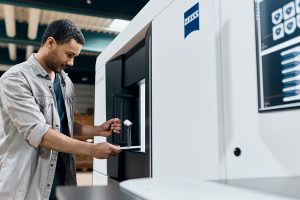
Inspecting electronic connector housings using CT technology
Identifying internal defects and correct connector pin positions of electronic connector housings is crucial for proper functioning of the final product. The advanced CT technology of ZEISS METROTOM 1 is the perfect fit to get deep insights of your electronic parts, allowing for quick and intuitive evaluation and improvement of production processes.
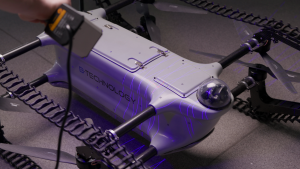
Changing the future of transportation with 3D scanning
B-TECHNOLOGY is transforming the future of transportation with an innovative flying-driving drone and the Beccarii car. Utilizing advanced 3D scanning, they ensure precision and quality in their groundbreaking designs.

Optimizing steam locomotives using hand-held 3D scanner
There is no Harz Mountains without the Harzer Schmalspurbahnen! This is why the company puts everything into maintaining their historic steam locomotives. How they do it? Using 3D scanning for efficient inspection of traditional vehicles.