The Danish company MarineShaft is a leading provider of repair and maintenance services for maritime components, including ship propulsion systems, propellers, shafts, and rudder equipment. The company offers both workshop-based and on-site repair services globally, ensuring flexible and efficient solutions tailored to customer needs.
One of MarineShaft’s key areas of expertise is the repair of large and complex maritime components that can be challenging to transport due to their size or weight. The ability to provide both on-site and in-house repair services allows MarineShaft to address technical problems quickly and effectively, regardless of the customer’s location.
Staying ahead of technological advancements is a priority for MarineShaft. Together with our Danish partner Zebicon they have studied their tasks intensively and looked for a suitable 3D scanning tool for them and found it in the ZEISS T-SCAN hawk 2. It has quickly become an integral part of on-site repair services they can provide. The 3D scanning technology enables precise measurement and analysis of large components directly on-site, enhancing the company’s capabilities in precision measurements and reducing repair times.
3D scanning supports a wide range of applications
MarineShaft uses 3D scanning technology to inspect and measure several key maritime components essential to their repair operations, including:
Propellers and propeller blades
3D scanning is utilized to verify the geometry of propellers and blades, ensuring uniformity and addressing issues such as vibrations or noise. This allows MarineShaft to detect damage or irregularities promptly, enabling precise decisions about repairs or adjustments.
Propeller cones and shafts
The technology is used to measure the dimensions of for instance cones on propeller shafts or propellers, ensuring precise geometry and fit of a new component with an existing one.
Rudder blades and rudder shafts
Rudder equipment, including blade and rudder stock, may be scanned on-site for accurate measurements. This can eliminate the need to move heavy components and ensure precise adjustments and repairs.
Crane foundations and other complex structures
3D scanning may also be used to measure e.g. crane foundations on ships. The technology enables evaluation of alignment and/or parallelism of surfaces and provide a decision basis for further repair actions.
By employing 3D scanning technology, MarineShaft can measure, analyze, and adjust these components efficiently, whether on land or at sea. The technology is applied both on-site and in-house, ensuring precision and efficiency when working with complex components.
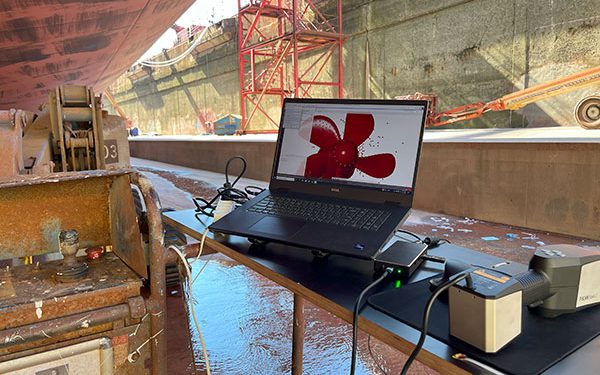
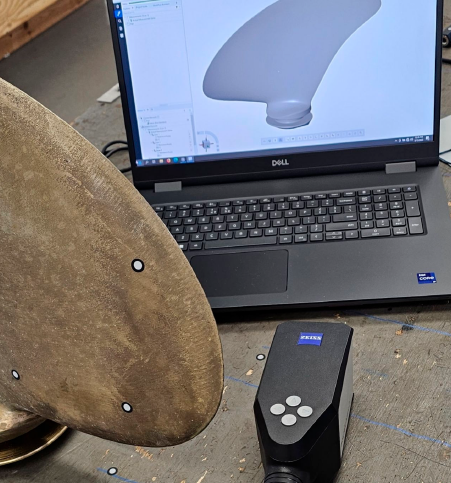
Solving challenges of large part inspection using 3D scanning
MarineShaft has resolved several key challenges in the repair of large maritime components through the use of 3D scanning technology, including:
Transportation
Heavy components such as rudder blades – can now be scanned on-site, removing the need for expensive transportation to workshops in some cases.
New measurement options
3D scanning introduces new measurement options like surface measurements, measurement of e.g. cylinders and cones, and measurement over relatively long distances on large components – all with high precision. This has not been possible with traditional manual measurements with various gauges and measuring tape.
Diagnostics & documentation
The technology has identified issues, such as inconsistent propeller blade geometries causing vibrations. This allows MarineShaft to visualize occurring defects to their customers using ZEISS INSPECT software and deliver targeted repair solutions based on state-of-the-art evaluation.
Operational efficiency
By handling 3D scanning and data processing internally, MarineShaft has eliminated delays and costs associated with third-party providers, improving efficiency and turnaround times. Automating reports and analyses has improved communication and operational efficiency.
This innovative approach has allowed MarineShaft to combine accuracy, speed, and cost-efficiency, reinforcing their position as a trusted leader in maritime repairs.
Endless inspection possibilities with 3D metrology
MarineShaft invested in 3D scanning technology by ZEISS to increase measurement capabilities, efficiency, and flexibility in their repair processes. The technology offers:
Virtual blue-fit tests
These enable simulation and optimization of component fits before production begins, ensuring seamless integration of new and existing parts.
Enhanced mobility
The portable equipment allows for on-site scanning anywhere in the world, eliminating the need to transport large and heavy components to a central workshop.
Improved process control
By reducing reliance on external providers, MarineShaft can manage scanning, data analysis, and repairs in-house, saving time and offering greater operational control.
This investment has improved customer satisfaction by reducing downtime, increasing repair quality, and enhancing flexibility in service delivery.
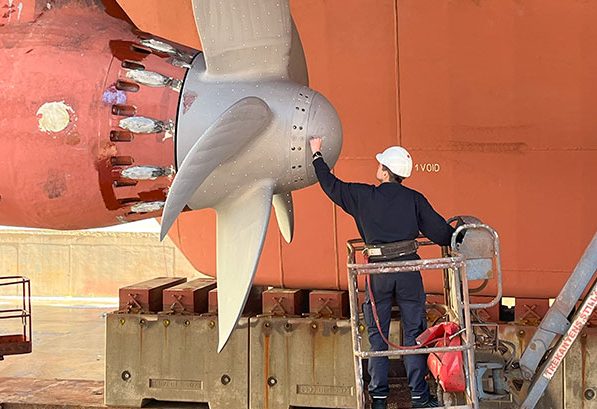
ZEISS T-SCAN hawk 2 for large repair projects on site
MarineShaft employs the portable 3D laser scanner ZEISS T-SCAN hawk 2 and TRITOP for 3D scanning.
The hand-held T-SCAN hawk 2 was chosen because it aligns perfectly with MarineShaft’s need for high-precision measurements, mobility, and flexibility. This device is particularly advantageous in challenging maritime environments. It enables on-site scans of both small components and large parts using powerful lasers and the satellite mode. Comprehensive statements of the part’s quality can be made by utilizing high-quality data.
The optical photogrammetry system TRITOP further supports measurements on relatively large components.
MarineShaft’s choice of a hand-held scanner reflects their commitment to providing fast, reliable, and customer-focused solutions while embracing technological innovation. Thus, efficient decision making of their customers has never been easier.
Everything we do is almost always urgent repairs, so time is crucial. That’s where 3D scanning can be very useful.
Hanne Magnussen - Head of Marketing at MarineShaft
Portable 3D scanning of large parts
Contact us now to book a free demo with our 3D scanning experts.