When our Italian partner Metrologia told us about this application story, we immediately knew that we were in for some exciting and forward-looking insights. As a long-standing member of our network, Metrologia always has its finger on the pulse and advises companies in all areas relating to industrial measurement technology. As a result, the Italian company Sabelt uses the 3D scanning solution in its production of vehicle seats and seat belts to ensure maximum safety in transportation.
Buckle up: the work at Sabelt
350 employees, 4 plants, 18 OEM customers worldwide – Sabelt is one of the well-known manufacturers for seats and seat belts. The company was founded in 1972 by Piero and Giorgio Marsiaj. Shortly after the company was founded, it turned out that they had the right instinct. The commitment from 1988 to use a seat belt led to considerable growth and increasing relevance of the company.
What started as an idea to maximize road safety, quickly evolved beyond the initial use of their products. In the 1990s, the company expanded into the motorsport sector and quickly became the go-to for seats, suits and accessories for high performance racing cars.
The company works to harmonize three key elements: economic growth, social inclusion and environmental protection. For this reason, it uses the latest technologies available.
Pier Carlo Barberis - Quality Manager at Sabelt
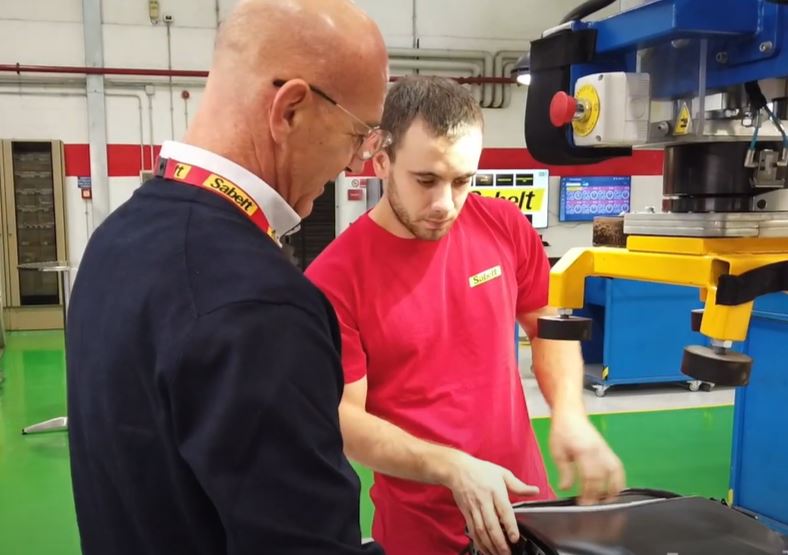
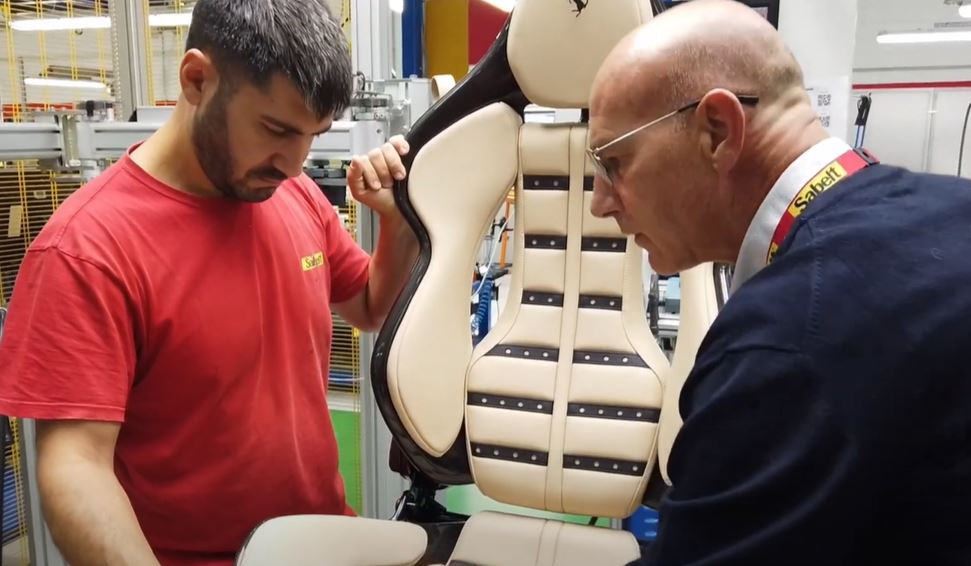
Its claim to be able to offer high-quality products is closely linked to intensive research and development investments. Around 8% of the company’s resources are therefore invested in improving quality, performance and safety. They are the only company in this field to carry out performance tests in their own dynamic test laboratory, which provides information about the strength of their production processes.
High quality standards meet
3D scanning
In order to complement these tests, they have been in contact with our partner Metrologia for a long time. They advised them intensively on the possibilities of integrating 3D scanning in the automotive sector. To be able to verify the multitude of different products in all phases of the product development process, the choice fell on
ZEISS T-SCAN hawk 2.
Its hand-held characteristics and flexibility allow to measure a wide range of parts, such as large surfaces of a seat as well as fine details of a seat belt. The generated 3D data is a highly precise representation of the original part. Deviations from CAD are made visible in no time. Even, if changes to some components are planned, these digital twins are the base for further alterations. ZEISS T-SCAN hawk 2 proves to be the perfect addition to quality management at Sabelt. The 3D scanner is used in the development phase, for measuring and analyzing parts and for the approval of supplied goods.
New Maker Portrait available
Want to know more about the story of Sabelt and their use of 3D scanning in the automotive sector? Watch the video here:
Sabelt: High performance seat belts for a safer future
Take a look behind the scenes at Sabelt, the Turin-based international market leader in high performance seat belts and manufacturer of outstandingly good car seats, race suits and other motorsport accessories. Their main goal? To harmonize the three key elements of their business: economic growth, social inclusion and environmental protection. The video shows you what our 3D scanner ZEISS T-SCAN hawk 2 has to do with it. Thanks to our Italian partner Metrologia SpA for sharing this story.
Want to learn more about Sabelt. Visit https://www.sabelt.com/